Conway Stewart’s current production techniques.
The casein protein is first extracted from skimmed milk through a chemical
process, precipitation. This separates the solid proteins from the milk
whey. The granular substance formed by the casein proteins is then carefully
dried to create the raw material for manufacturing process.
The casein granules are graded depending on their ‘transparent’
quality, and then most appropriate grade selected for the finished product.
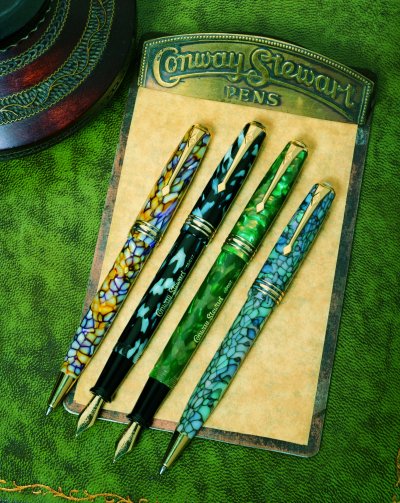
The modern Conway Stewart casein
collection
The first step in manufacturing process is to grind the casein to an
evenly powdered form between steel rollers and sieves. The casein is then
swollen and softened in water, coloured with dyes and rendered even transparent
or opaque depending on requirements.
The swollen granules are then laid flat and pressed into a slab form measuring
16" x 19" and 1" deep. Only 1mm per week can be ‘laid
down’ in order that the casein bonds effectively. Therefore it takes
16 weeks for the thickness required for a pen barrel. The material is
then placed in tanks of diluted Formalin, the action of which gives casein
it’s hard tough nature. Kept at room temperature, the reaction is
slow! It can take several weeks to harden a thin sheet and up to 3 months
to harden a 16mm sheet.
On removal from the Formalin tank, the drying process is carried out in
carefully designed drying chambers with a rigidly controlled airflow to
maintain the ideal moisture content of 6% in the material.
The manufacture of casein is now complete. Each batch of casein is unique
as once a batch of casein is made it is impossible to reproduce exactly.
Why did Conway Stewart favour casein?
I can find no definitive statements as to why Conway Stewart used casein
in so many of their models from the late 1920’s through to the 1950’s.
Maybe it was because of the interesting and varied colours and patterns
made available through the use of this material. Perhaps it was because
they had difficulties in acquiring celluloid rod stock or was it that
celluloid was too expensive?

Conway Stewart Dinkie Halloween
What is known is that Conway Stewart was almost unique in their adoption
of this material in the European arena. Few pens can be found made from
casein from European manufacturers and the same can be stated for the
manufacturers in the USA.
Today the new Conway Stewart company have revived this adoption of casein
in their range of modern designs and interestingly so have some other
European manufacturers, albeit to a much lesser extent.
Don Yendle, President of Conway Stewart Ltd also comments
on this discussion.
What is not covered here is the Japanese producer of Casein who has been
going as
long, if not longer, that the European makers. They are still in production
and have around 10 massive machines which are specialised in producing
up to
10 colour casein by helical screw extrusion process.
I believe Conway Stewart favoured casein purely because they wanted to
achieve the most dramatic colour finishes possible. I have talked to people
in their 80's who worked for BX and Erinoid, all of whom remember supplying
CS with the product. The last Erinoid machine is still in operation in
Holland still making button blanks (as are the Japanese). We have some
Japanese casein stock from 1940 which we will shortly be using.
Casein can be stabilised by 'training', and most of the problems encountered
by Sheaffer etc., were due to using casing which had not been cured and
then
'trained', casein starts life as a sheet as we all know, unless you are
extruding it of course, as a sheet the material thinks its square, and
when
moisture attacks the material tries to return to its original shape. We
use
5 different processes to 'train' the casein, and for the past 6 years
we
have been developing a new process which renders the casein resistant
to
water. This method will be used on the new production planned for this
year.
Of course, as stated, we have to put our casein colours into production
some
18 months before the intended launch date. 'New' casein under a year old
will warp very quickly. Moisture content should be 6% with a 3% allowable
swing either way, which means threads and fitments must take this moisture
swing into account, so most of it's in the engineering standards.
References:
David Wells Vintage Pens
Jonathan
Donahaye Conway Stewart Collection
Conway
Stewart history
Home of the Plastics Historical Society
|